In 3D printing, nozzle size plays a pivotal role in balancing speed, material flow, and print quality. Larger nozzles allow faster printing but reduce detail, while smaller ones enhance resolution.Choosing the right nozzle ensures optimal results.
Key Takeaways
- Pick the right nozzle size for speed and detail balance. Small nozzles give better detail but print slower. Big nozzles print faster but may lower quality.
- Know the material when choosing a nozzle. Soft filaments work well with big nozzles. Hard materials need small nozzles for fine details.
- Try common nozzle sizes, like 0.4 mm, to see what works best. This improves print quality and keeps extrusion steady.
How nozzle size impacts 3D print quality

Layer thickness and resolution
The nozzle size directly determines the layer thickness, which is a critical factor in achieving higher resolution prints. Smaller nozzles, such as 0.25 mm, allow for thinner layers, resulting in finer details and smoother surfaces. This makes them ideal for intricate designs or models requiring high precision. On the other hand, larger nozzles, like 0.8 mm, produce thicker layers, which can compromise resolution but significantly reduce print time.
The relationship between nozzle diameter and layer height can be summarized in the table below:
Nozzle diameter (mm) |
Min. layer height (mm) |
Standard layer height (mm) |
Max. layer height (mm) |
---|---|---|---|
0.25 |
0.06 |
0.13 |
0.2 |
0.4 |
0.1 |
0.2 |
0.32 |
0.6 |
0.15 |
0.3 |
0.48 |
0.8 |
0.2 |
0.4 |
0.64 |
For projects requiring higher resolution prints, selecting a smaller nozzle is essential. However, keep in mind that thinner layers may lead to longer print times and increased material usage due to potential over-extrusion.
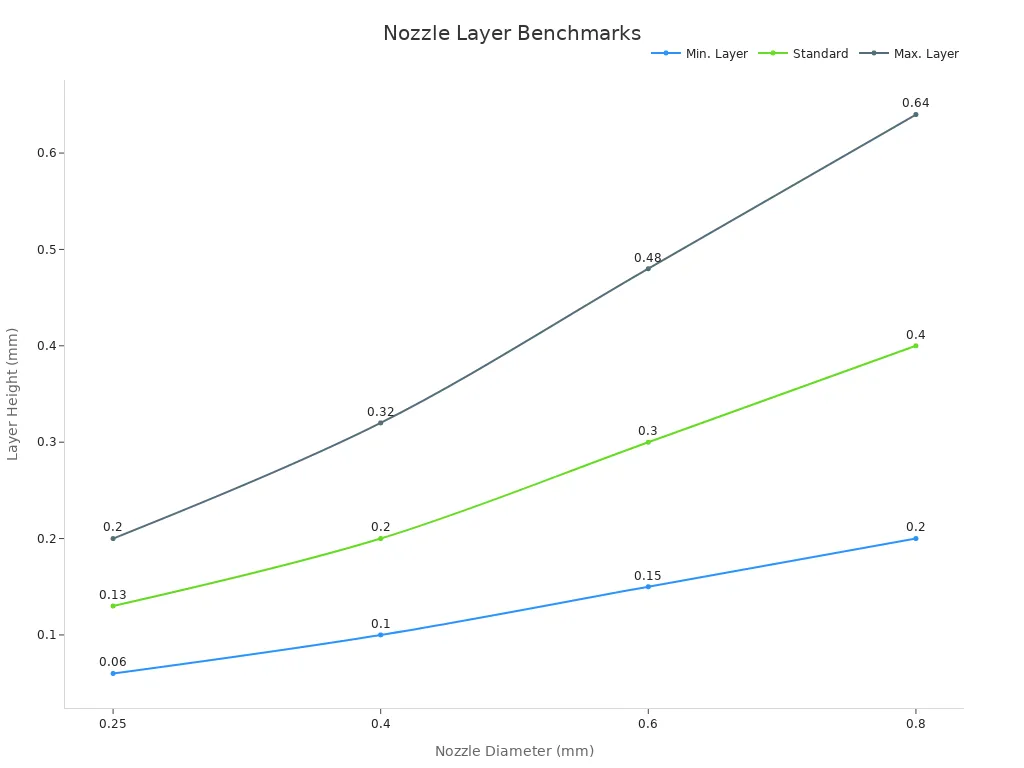
Print speed and efficiency
Nozzle size also influences the speed and efficiency of 3D printing. Larger nozzles extrude more material per pass, enabling faster print times. This makes them suitable for large-scale projects or prototypes where detail is less critical. Conversely, smaller nozzles require more passes to cover the same area, which slows down the process but enhances detail and layer adhesion.
Research findings highlight the trade-offs between nozzle size and efficiency:
- Smaller nozzle diameters (10 mm) resulted in a fracture strength increase of up to 30% compared to larger nozzles (40 mm).
- Fiber alignment was more influenced by smaller nozzle diameters, while larger nozzles (greater than 20 mm) had negligible effects on fiber alignment.
- No significant correlation was found between print speed and efficiency in terms of fiber alignment and fracture strength.
When balancing speed and quality, consider the project's requirements. For functional parts where strength and adhesion are priorities, a medium-sized nozzle (e.g., 0.4 mm) often provides the best compromise.
Material flow and extrusion consistency
The nozzle size affects material flow and extrusion consistency, which are crucial for maintaining print quality. Smaller nozzles require precise control of material flow to prevent under-extrusion or clogging. They also create higher pressure in the liquefier region, which can impact extrusion rates. Larger nozzles, while less prone to clogging, may struggle with maintaining consistent flow at higher speeds.
Studies have shown that:
- Smaller nozzle diameters combined with reduced strand layer heights lead to improved porosity and bond line densities in 3D printed cross sections.
- The pressure drop from the inlet to the outlet of the liquefier region varies significantly with changes in nozzle diameter.
- Under-extrusion rates were similar for different hot ends at lower feed rates but varied at higher rates, with the v6 Gold showing the least under-extrusion.
To achieve consistent extrusion, match the nozzle size with the material's properties and the printer's capabilities. For example, flexible filaments may perform better with larger nozzles, while rigid materials benefit from smaller ones for finer detail.
Factors to consider when selecting a nozzle size

Project type and level of detail
The type of project you are working on and the level of detail required play a significant role in determining the optimal nozzle size. Larger nozzles, such as 0.6 mm, are ideal for printing large parts or prototypes where speed is a priority. They can reduce print time by nearly 50% compared to standard nozzles, but they may compromise surface smoothness and detail. Smaller nozzles, like 0.2 mm, are better suited for intricate designs or models requiring higher resolution prints. However, they increase print time by approximately 30% compared to a 0.4 mm nozzle.
Layer height also affects the final appearance of your 3D print. Thinner layers, such as 0.1 mm, produce smoother finishes and finer details, making them perfect for decorative or display pieces. In contrast, thicker layers, like 0.3 mm, result in rougher surfaces and more visible layer lines but significantly reduce printing time. For example, a model printed with a 0.1 mm layer thickness might take 8 hours, while the same model printed with a 0.3 mm layer thickness could take only 3 hours. Balancing these factors is essential to achieve optimal results for your specific project.
Material properties and compatibility
The material you choose for 3D printing must be compatible with the nozzle size to ensure consistent extrusion and high-quality prints. Flexible filaments, such as TPU, often perform better with larger nozzles because they require less precision and are less prone to clogging. Rigid materials, like PLA or ABS, benefit from smaller nozzles, which allow for finer detail and better layer adhesion.
Each material has unique flow characteristics that influence how it interacts with the nozzle. For instance, materials with higher viscosity may struggle to flow consistently through smaller nozzles, leading to under-extrusion or clogging. On the other hand, low-viscosity materials may flow too quickly through larger nozzles, resulting in over-extrusion and reduced print quality. Matching the nozzle size to the material's properties ensures consistent extrusion and optimal results.
Strength, speed, and resolution trade-offs
Choosing the right nozzle size involves balancing strength, speed, and resolution. Smaller nozzles allow for finer details and higher resolution prints but require slower speeds and may increase the risk of clogs. Larger nozzles enable faster printing and stronger layer bonding but may compromise detail and surface quality.
The trade-offs between these factors can be summarized as follows:
Aspect |
Trade-off Description |
---|---|
Layer Thickness |
Thinner layers enhance detail but increase print time and error potential. |
Print Speed |
Faster speeds reduce print time but may compromise layer bonding and detail quality. |
Nozzle Size |
Smaller nozzles allow for finer details but may lead to clogs and require slower speeds. |
Application Specificity |
Higher resolutions are necessary for detailed models, while lower resolutions may suffice for less detail. |
For functional parts where strength and durability are critical, a medium-sized nozzle, such as 0.4 mm, often provides the best balance. For decorative items or models requiring intricate details, smaller nozzles are the better choice. Understanding these trade-offs helps you make informed decisions and achieve the desired 3D print quality.
Practical advice for choosing the right 3D printer nozzle size
Experimenting with standard nozzle sizes
Standard nozzle sizes, such as 0.4 mm, offer a versatile starting point for most 3D printing projects. These nozzles balance speed, resolution, and adhesion, making them suitable for a wide range of applications. Experimenting with these sizes allows you to understand how different materials behave under varying conditions. For instance, flexible filaments like TPU often perform better with larger nozzles, while rigid materials like PLA excel with smaller ones.
Optimized nozzle designs can also improve extrusion performance. Studies show that reducing recirculation size minimizes clogging and material degradation. A table below highlights how nozzle adjustments impact pressure drop across different materials:
Material |
Pressure Drop Improvement |
Reference Figure |
---|---|---|
PA6/66 |
Figure 10 |
|
PET-G |
65% |
Figure 10 |
PC |
Not specified |
Figure 10 |
PET-CF |
Insensitive |
Figure 10 |
Experimenting with standard sizes helps you identify the ideal nozzle size for achieving desired print quality and extrusion consistency.
Balancing speed and detail
Balancing speed and detail requires careful consideration of nozzle size. Larger nozzles, such as 0.8 mm, extrude more material per pass, enabling faster printing. However, they may compromise fine detail and resolution. Smaller nozzles, like 0.2 mm, enhance accuracy but demand slower speeds to maintain consistent filament flow.
Research indicates that increasing nozzle diameter leads to wider rubber lines, enhancing speed but reducing detail accuracy. Conversely, smaller nozzles improve shape precision but require slower printing speeds. An optimal nozzle size of 0.85 mm strikes a balance between speed and detail, making it suitable for projects requiring both efficiency and quality.
When selecting a nozzle, consider the project's requirements. Functional parts benefit from medium-sized nozzles for strength and adhesion, while decorative items demand smaller nozzles for intricate designs.
Troubleshooting nozzle-related issues
Nozzle-related issues, such as clogging or inconsistent extrusion, can affect print quality. Addressing these problems involves understanding the relationship between nozzle size and material properties. Smaller nozzles create higher pressure in the liquefier region, increasing the risk of clogs. Larger nozzles reduce clogging but may struggle with maintaining consistent flow at higher speeds.
To troubleshoot effectively:
- Inspect the nozzle regularly for debris or wear.
- Adjust print settings to match the material's viscosity and flow characteristics.
- Experiment with feed rates to minimize under-extrusion or over-extrusion.
Optimized nozzle designs reduce pressure drop and improve extrusion performance, ensuring consistent results. Matching nozzle size to material and printer capabilities helps you avoid common issues and achieve desired print quality.
Selecting the right nozzle size is essential for achieving optimal 3D print quality and efficiency.
- Smaller nozzles produce higher-resolution prints with smoother finishes, while larger nozzles enable faster printing but sacrifice detail.
- Nozzle size also affects layer adhesion, filament width, and material compatibility, making it a critical factor in print success.
Nozzle Size |
Benefits |
Trade-offs |
---|---|---|
Smaller Nozzle |
Better detail, smoother finish |
Slower print time, fragile parts |
Larger Nozzle |
Faster printing, stronger parts |
Reduced detail, slower linear speeds |
Experimentation and understanding your project’s needs will help you make informed decisions.
FAQ
What is the best nozzle size for beginners?
A 0.4 mm nozzle is ideal for beginners. It balances speed, detail, and ease of use, making it suitable for most materials and projects.
How often should you replace a 3D printer nozzle?
Replace your nozzle every 3-6 months or after heavy use. Frequent clogs, inconsistent extrusion, or visible wear indicate it’s time for a replacement.
Can you use the same nozzle for all materials?
No, some materials require specific nozzle sizes. For example, abrasive filaments like carbon fiber need hardened nozzles, while flexible filaments work better with larger diameters.
Leave a comment
All comments are moderated before being published.
This site is protected by hCaptcha and the hCaptcha Privacy Policy and Terms of Service apply.